Preventive concrete protection
According to "statista.com", there will be 9400 biogas plants in Germany alone in 2020. All these plants in the agricultural, waste and energy industries face the same challenge: BSK, or Biogenic sulphuric acid corrosion (see below).
Well-designed
desulphurisation and preventive coating of the concrete are
the ideal. The photos opposite show examples of such a
coating. The plastic foil for concrete protection was
concreted into both reinforced concrete tanks.
Concrete protection through coating
Concrete protection foil and plates - From experience we say: in the total package, the best coating.
Essentially, there are four systems with which reinforced concrete containers can be protected against damage caused by acid attacks or the likes. The protection of the concrete is achieved by painting, coating or covering. Coating is done with a chemically resistant protective layer. In this protective layer, the sealing, is applied either directly when the container is concreted or subsequently.
Specialisation
The company "Spezialmontagen-John" specialises in the subsequent lining or coating of reinforced concrete tanks with PP or PE films, and in particular fermenters and fermentation residue end stores of biogas plants.
Subsequent cladding of reinforced concrete tank ceilings
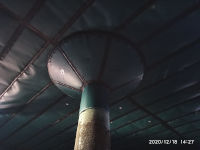
Subsequent wall cladding
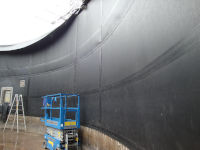
Waterproofing and cladding of the floor
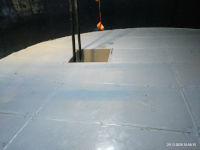
All with polymer protective films. Why? More on that below.
1. Plastic films and sheets
MERITS:
- Plastic films and sheets made of polypropylene (PP) or
polyethylene (PE) are absolutely resistant to chemical
attack.
- The films are mostly standard films/sheets from various
manufacturers and prices
- Can be applied in almost any weather and temperature
- The substrate does not have to be specially pre-treated,
washing off with a high-pressure cleaner is sufficient
(provided that the building has been repaired, of course)
- the material thickness of the coating is always the same
DEMERITS:
- If you want to work on large areas, you need lifting
equipment (crane).
2. Epoxy resin
Coatings with epoxy resin were especially processed in the early years of the biogas boom.
MERITS:
- Absolutely resistant to chemical attacks
- Processing is possible without special tools
DEMERITS:
- Processing is very labour-intensive
- It is only possible under ideal conditions
- Temperature dependent
- Weather dependent
- Substrate must be absolutely dry and clean (water
blasting, sand blasting)
- The resin is very brittle and can tear easily - it is
then infiltrated ...
3. Polymer silicate
This coating is mainly used in sewage construction.
MERITS:
High resistance to acids, solvents, oils and greases.
DEMERITS:
- Processing is very labour-intensive
- Only possible under ideal conditions
- Temperature dependent
- Weather dependent
- Substrate must be absolutely dry and clean (water
blasting, sand blasting)
4. Polyurethan
Diese Form der Beschichtung ist funktioniert gut, aber auch hier gibt es in der Verarbeitung liegend einige Probleme.
MERITS:- Permanently elastic and very durable
DEMERITS:
- Processing only possible with special machines -
Processing is very labour-intensive
- Only possible under ideal conditions
- Temperature dependent
- Weather dependent
- Substrate must be absolutely dry and clean (water
blasting, sand blasting)
Biogenic sulphur corrosion
The operation of a fermenter, a fermentation tank or a closed wastewater system uses biochemical processes whose reaction products can have a destructive effect on the structure of the reinforced concrete tanks. The best protection against these damaging effects is to counteract them in advance. The problem arises from sulphur, which is inevitably introduced into the system. So desulphurisation would be the ideal way to go
The sulphur
If desulphurisation is incomplete in the gas space or if small amounts of oxygen remain in the gas space due to uneven distribution of the oxygen added for desulphurisation, a strong chemical attack on the concrete in this area can occur.
Some biochemistry
Where does sulphur come from? The answer is: sulphur-containing amino acids - cysteine and methionine. Both amino acids contain one sulphur atom each. Methionine is a precursor of the amino acids cysteine and taurine and of the antioxidant glutathione. The metabolically active form of methionine is S-adenosyl-methionine, which is found in practically all body tissues and fluids and is essential for the construction of proteins. It is needed for the synthesis, stimulation and breakdown of many substances in the body. It contributes to the formation of adrenaline, carnitine, choline, creatine, melatonin and nucleic acids. When a protein is built in a living organism, this process always begins with methionine as the starting building block. Afterwards, methionine is usually separated from the finished protein. The sulphur atom is needed not only for building but also for stabilising protein structures.
Hydrogen sulphide escaping from the substrate is converted by bacteria of the genus Thiobacillus into sulphurous acid or sulphuric acid as a metabolic end product. Another part of the sulphur is deposited on the surfaces in the gas space in the form of elemental sulphur (see photo). These bacteria are found on moist surfaces in the gas space. The metabolic process causes the pH value to drop below pH 1, which is a very strong sulphuric acid attack on cement-bound and on metallic construction and materials, such as steel, cast iron, zinc, copper, nickel, chrome and aluminium.
TOP